A fuel injection pump in internal combustion engines is responsible for delivering high-pressure fuel to the engine’s fuel injectors. It is a common component in diesel engines and some gasoline direct-injection engines.
LINK TO FUEL DELIVERY SYSTEMS. -; BAD FUEL PUMP SYMPTOMS
The fuel injection pump precisely meters and times the delivery of fuel. It ensures that fuel is injected into the combustion chamber at the optimal moment within the engine cycle and in the correct amount for efficient combustion.
Fuel injection pumps are driven by the engine’s camshaft or a dedicated drive mechanism. The drive mechanism ensures that they generate extremely high pressures to atomize the fuel properly for mixing with air.
Diesel engines require higher pressures compared to gasoline engines. Therefore, the fuel injection pump in diesel engines is often more complex and robust.
The precise operation of the fuel injection pump is essential for proper engine performance, fuel efficiency, and emissions control. Because, the fuel injection pump is responsible for delivering fuel to your engine with utmost accuracy.
It acts as a reliable conductor, ensuring that each cylinder receives an optimal amount of fuel at precisely the right moment. This precise and efficient delivery not only enhances performance but also contributes to improved fuel economy.
Whether you’re driving a gasoline or diesel-powered vehicle, understanding how the fuel injection pump works is essential. From direct injection high-pressure pumps to automatic fuel transfer systems, the role of these pumps is in maintaining a steady supply of fuel to your injectors.
Function and how fuel injection pumps work.
The fuel injection pump within any internal combustion engine converts fuel into a fine mist that can be easily used for combustion. This ensures optimal power, performance, and efficiency of the engine.
The engine is able to figure out the right amount of fuel to use for each combustion cycle when the fuel injection pump is working properly.
This ensures that the engine receives an adequate supply of fuel, allowing it to generate sufficient power for acceleration and overall performance. On the other hand, if the fuel injection pump becomes faulty or malfunctions, it can have detrimental effects on the engine’s performance.
Poor acceleration is one common symptom of a faulty pump as it fails to deliver an adequate amount of fuel to support efficient combustion. An improperly functioning pump can lead to increased emissions due to incomplete combustion.
Ensuring that your vehicle’s fuel injection pump is in good working condition maintains power, performance, and efficiency while minimizing emissions. Regular maintenance and inspections by qualified professionals can help identify any issues with the pump early on and prevent potential problems down the road.
Detailed explanation of the working principles of fuel injection pump.
The fuel injection pump ensures that the engine receives the right amount of fuel at the correct pressure and timing. Modern vehicle fuel systems use electronic control to optimize engine performance, efficiency, and emissions.
1). Fuel delivery process.
During the internal combustion engine intake stroke, the plunger moves down, creating a vacuum in the barrel. This vacuum draws fuel from the fuel tank into the pump through the fuel inlet.
Fuel delivery process during the compression stroke involves camshaft rotation which pushes the plunger upwards. The upward movement of the plunger compresses the fuel in the barrel. As pressure builds, the delivery valve opens, allowing fuel to flow into the injector.
Fuel injection delivery process goes through the injector which atomizes the fuel and sprays it into the combustion chamber. The timing of this injection is critical for optimal combustion and is synchronized with the engine’s crankshaft position.
2). Control of fuel quantity and timing.
Governor mechanism of the fuel pump injection adjusts the amount of fuel delivered based on engine speed and load. At higher speeds, it reduces the fuel quantity to prevent over-revving. However, at lower speeds or under high load, it increases the fuel quantity for more power.
The timing mechanism of the fuel pump injection allows precise timing with the engine’s camshaft. This ensures that fuel is injected at the optimal point in the combustion cycle, usually just before the piston reaches top dead center (TDC) on the compression stroke.
3). High-pressure generation by the injection fuel pump.
The movement of the plunger inside the barrel generates high pressure. The high pressure is necessary to atomize the fuel properly as it enters the combustion chamber.
In modern fuel delivery systems like the common rail, the pump maintains a reservoir of high-pressure fuel. This fuel is then distributed to individual injectors, allowing for very precise control over injection timing and quantity.
4). Injection control in electronic fuel systems.
Sensors and actuators are found in modern fuel injection systems. These systems use electronic control units (ECUs) to manage fuel delivery.
Sensors provide real-time data on engine speed, temperature, air intake, and other parameters. Afterwards, the ECU processes this data and adjusts the fuel injection pump and injectors accordingly.
The role of timing and metering in fuel injection.
Timing and metering roles in fuel injection systems ensures that the engine receives the right amount of fuel at the precise moment for efficient combustion. Overall, timing and metering are critical aspects of fuel injection systems that directly impact engine performance, efficiency, and emissions control.
Timing in internal combustion engines.
Timing refers to the precise moment when the fuel is injected into the combustion chamber relative to the position of the piston. It helps in optimizing combustion efficiency, power output, and emissions control.
The timing of fuel injection must be synchronized with the engine’s crankshaft position to ensure that fuel is injected at the optimal point in the combustion cycle. Injecting fuel too early or too late can result in incomplete combustion, reduced power, increased emissions, and engine knock. Therefore, accurate timing is essential for maximizing engine performance and efficiency.
Metering in internal combustion engines.
Metering involves controlling the quantity of fuel delivered to the combustion chamber during each injection event. The amount of fuel injected must be precisely metered to match the engine’s operating conditions, such as engine speed, load, and temperature.
This ensures that the air-fuel ratio remains within the optimal range for combustion. Modern fuel injection systems use sophisticated metering techniques.
For example, pulse width modulation in electronic systems, to precisely control the duration that the fuel injectors remain open. By accurately metering the fuel, the engine can achieve optimal fuel economy, power output, and emissions performance under various operating conditions.
Exploring fuel injection system components.
Some of the components of the fuel injection system are injectors, pressure regulators, sensors, plungers and barrels, camshafts, fuel inlets and outlets among others that we’re going to look into.
The fuel injection system of modern internal combustion engines, ensures optimal performance and efficiency. A closer look at its various components and their roles will help us understand how this system works.
1). Injectors.
Injectors are one of the key components of the fuel injection system. These small nozzles spray precise amounts of fuel into the engine cylinders at high pressure.
By atomizing the fuel, injectors ensure efficient combustion and power generation. They play a crucial role in maintaining the correct air-fuel mixture for different engine conditions.
2). Pressure regulators.
Pressure regulators help maintain consistent fuel pressure within the system. They ensure that an appropriate amount of fuel reaches the injectors, regardless of variations in demand or engine load.
The pressure regulators contribute to smooth engine operation and prevent potential damage caused by excessive or insufficient fuel supply by regulating the pressure.
3). Sensors.
Sensors are integral to monitoring and controlling various aspects of the fuel injection system. They provide important feedback to the engine control unit (ECU).
Afterwards, this feedback allows the ECU to adjust fuel delivery based on factors like throttle position, air intake temperature, and oxygen levels in exhaust gases. This continuous monitoring ensures optimal performance under different operating conditions.
4). Basic fuel injection components and their functions.
- Plunger: A cylindrical component that moves up and down to create pressure.
- Barrel: The cylindrical chamber in which the plunger moves.
- Delivery Valve: Ensures one-way flow of fuel into the injector.
- Camshaft: Drives the plunger through mechanical linkages.
- Fuel Inlet: Where fuel enters the pump from the fuel tank.
- Fuel Outlet: Where pressurized fuel exits the pump to the injector.
- Governor: Regulates the fuel quantity based on engine speed and load.
The fuel injection system delivers precise amounts of fuel to each cylinder for efficient combustion. These components and other elements like the fuel tank and associated plumbing ensure proper functioning of the fuel injection system. Hence, resulting in improved power output, reduced emissions, and better overall vehicle performance.
Components and replacement parts.
There is a wide variety of replacement parts available in the market. These parts cater to different engine components and ensure smooth functioning of the fuel injection system.
Options include OEM parts that are specifically designed for compatibility and reliability with your vehicle’s engine. These original equipment manufacturer (OEM) parts are known for their high quality and performance.
Aftermarket components are also available, offering cost-effective alternatives without compromising on functionality.
Regular maintenance helps prolong the lifespan of components. This includes periodic inspections, cleaning of the vehicle fuel system, and replacing worn-out components.
Maintenance tasks may involve checking valves, filters, cylinders, and other integral parts of the system. By addressing any issues promptly, you can prevent potential damage to both the pump and the engine.
Types of fuel injection pumps.
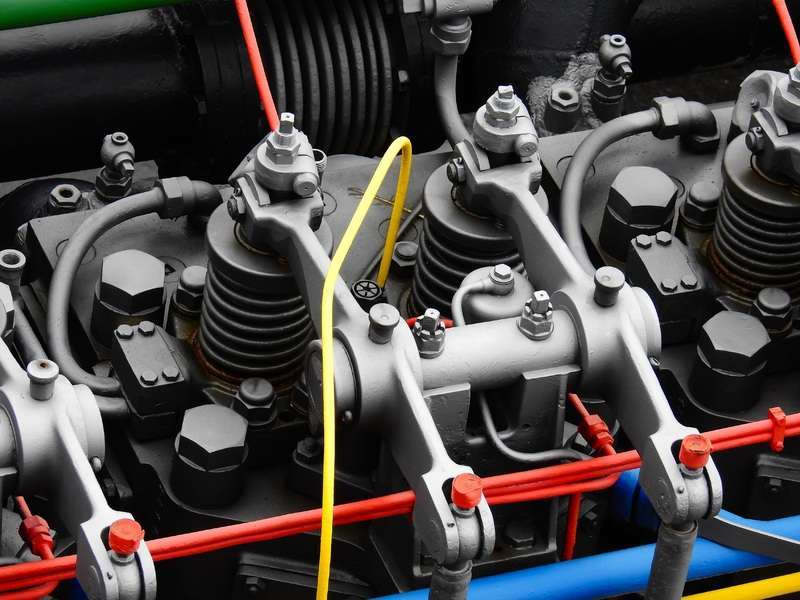
The different types of fuel injection pumps are in-line fuel injection pump, rotary fuel injection pump, common rail fuel injection pump, mechanical fuel injection and electronic fuel injection.
Each type of fuel injection pump has its own set of characteristics, making it suitable for specific applications and engine types. Understanding these differences helps in selecting the right pump for your vehicle or machinery, hence, ensuring optimal performance and reliability.
1). In-line fuel injection pump.
The in-line fuel injection pump has multiple plungers arranged in a line, each corresponding to a cylinder in the engine. It is commonly used in older and large diesel engines.
In-line fuel injection pump is durable and capable of high-pressure fuel delivery. Additionally, it is larger and heavier in comparison to other types and with more complex maintenance requirements.
2). Rotary (Distributor) fuel injection pump.
Rotary fuel injection pump uses a single plunger and a rotating distributor to deliver fuel to each cylinder in turn. It is often found in medium to small diesel engines.
The rotary fuel injection pump is more compact and lighter than in-line pumps. It may have lower durability and pressure capability when compared to in-line pumps.
3). Common rail fuel injection pump.
Its name is because it delivers fuel into a common rail, that is a shared high-pressure reservoir, from which the fuel is distributed to individual injectors.
The common rail fuel injection pump is widely used in modern diesel engines and some gasoline direct-injection systems. It provides precise fuel delivery, higher pressure, and improved emissions control.
Common rail fuel injection pump is more complex and expensive in comparison to other fuel pumps and it requires high-quality fuel and maintenance.
4). Unit injector pump (UI).
The unit injector pump integrates the pump and injector into a single unit mounted directly on the engine. It is commonly used in heavy-duty diesel engines, such as those in trucks and industrial applications.
Despite its complex design and potentially higher repair costs, the unit injector pump offers high injection pressure and precise control.
5). Electronic unit injector pump (EUI).
The electronic unit injector pump is similar to the unit injectors but with electronic control for more precise fuel delivery. It is used in modern diesel engines for improved performance and emissions control.
Although it requires advanced electronic control systems which increases its complexity and cost, the electronic unit injector pump offers enhanced precision and efficiency.
6). Mechanical fuel injection pump.
Mechanical fuel injection pump uses mechanical linkages and timing devices to control fuel delivery. It is common in older diesel engines and some vintage gasoline engines.
The mechanical fuel injection pump has a simple and robust design. Therefore, it offers less precise control over fuel delivery and timing when compared to electronic systems.
7). High-pressure fuel pump (HPFP).
High pressure fuel pump is used in gasoline direct injection (GDI) systems to deliver fuel at very high pressures. It enables more efficient combustion in modern gasoline engines with direct injection and offers better performance.
However, the high pressure fuel pump acquisition and installation is at a high cost and these pumps have sensitivity to fuel quality.
Upgrading fuel pumps for improved performance.
High-performance fuel pumps significantly enhance the power output of your vehicle by increasing the fuel flow rate. These upgraded pumps improve throttle response and deliver a more efficient fuel supply to the engine.
Firstly, you’ll need to choose the right type of pump for your specific needs. Whether you’re running on diesel or gasoline, there are different options available that cater to each fuel type’s requirements.
Some vehicles require specific fuel pumps designed to meet their unique specifications. It’s essential to ensure compatibility with your vehicle model before making any upgrades.
Upgrades to your fuel system may also necessitate additional modifications or tuning. For instance, installing a high-pressure delivery will help optimize performance by ensuring an adequate supply of fuel at all times.
Similarly, adding extra-long hoses or upgrading fuel filters can improve overall efficiency and protect the engine from contaminants.
By upgrading your fuel injection pump and considering other related components such as filters and hoses, you can unlock improved performance and responsiveness from your vehicle’s engine.
Factors to consider when choosing the right fuel injection pump.
Some of the factors to consider when choosing the right fuel injection pump are engine type, fuel system design, fuel type compatibility, environmental conditions, quality and brand reputation.
Choosing the right fuel injection pump for your engine is crucial for optimal performance and longevity. Here are several factors to consider when making this decision.
1). Engine type and specifications.
Ensure the fuel injection pump is compatible with your engine type; either diesel or gasoline. Additionally, ensure the fuel injection pump meets the specific requirements of your engine’s make and model.
2). Fuel system design.
Consider whether your engine uses a common rail, direct injection, or multi-point fuel injection system, because the pump must match the system design.
3). Pressure and flow rate requirements.
Verify that the fuel injection pump is capable of delivering the required fuel pressure and flow rate to meet your engine’s performance demands, especially under high-load conditions.
4). Quality and brand reputation.
Choose pumps from reputable manufacturers known for producing high-quality and reliable vehicle fuel system components. Research reviews and ratings to ensure the pump’s durability and performance.
5). OEM vs. aftermarket.
Decide between an Original Equipment Manufacturer (OEM) pump, which is designed to meet the exact specifications of your vehicle, and an aftermarket pump, which offers enhanced features or cost savings.
6). Fuel type compatibility.
Ensure the pump is compatible with the type of fuel you use. For example, standard gasoline, diesel, biodiesel, or ethanol blends.
7). Environmental conditions.
Consider the environmental conditions the pump will be exposed to, for example, extreme temperatures or high altitudes, and choose a pump that performs reliably under these conditions.
8). Electrical requirements.
Check the pump’s electrical specifications, for example, voltage and current requirements. Ensure that the fuel pump is compatible with your vehicle’s electrical system.
Importance of fuel injection pump.
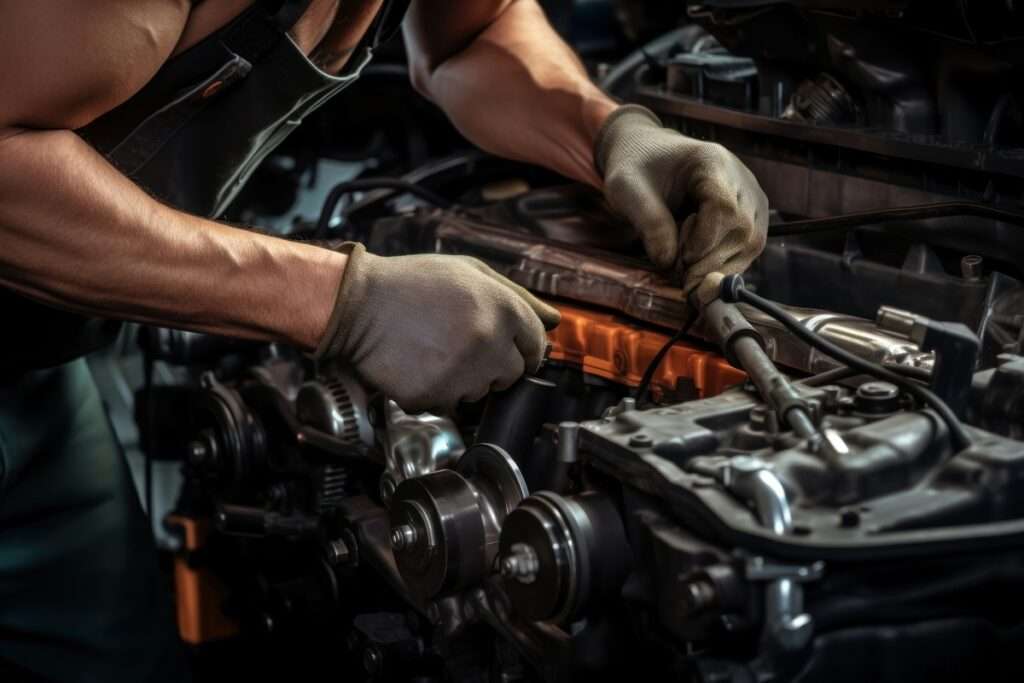
The importance of a fuel injection pump include efficient fuel delivery, better throttle response, power output and optimal combustion. It’s clear just how crucial a fuel injection pump is for your vehicle’s performance.
A properly functioning fuel injection pump ensures efficient delivery of fuel to the engine, resulting in optimal combustion and power output. Whether you’re looking to replace a faulty pump or upgrade to enhance your vehicle’s performance, investing in a high-quality fuel injection pump is essential.
To ensure you choose the right fuel injection pump, consider factors such as compatibility with your vehicle’s make and model, durability, and reputation of the manufacturer. Remember that a reliable fuel injection pump significantly improves your engine’s efficiency and overall driving experience.
Impact on engine performance and emissions.
A fuel injection pump affects engine performance through precise fuel delivery, engine efficiency, power out-put, emissions control and cold start performance. It significantly affects engine performance by precisely controlling the delivery of fuel into the combustion chambers.
1). Fuel delivery precision.
The fuel injection pump ensures that the correct amount of fuel is delivered to the engine cylinders at the right timing within the internal combustion engine cycle. This precision improves combustion efficiency, resulting in more power and better throttle response.
2). Optimized fuel-air mixture.
By delivering fuel in a finely atomized spray, the pump helps achieve an optimal fuel-air mixture. This leads to more complete combustion while enhancing engine performance and reducing unburned fuel emissions.
3). Engine efficiency.
Properly timed fuel injection helps maintain efficient engine operation. Consistent and accurate fuel delivery reduces fuel consumption and increases miles per gallon (MPG), making the engine more economical.
4). Power output.
A well-functioning fuel injection pump contributes to maximum engine power by ensuring that fuel is available when the engine demands it. This is very important especially under high load or acceleration conditions.
5). Smooth engine operation.
The pump maintains a steady and precise fuel flow which helps the engine run smoothly and reduces instances of engine knock, misfires, and rough idling. This contributes to a smoother driving experience.
6). Emission control.
Accurate fuel injection timing and metering are useful in controlling emissions. Proper combustion reduces the production of harmful pollutants such as NOx, CO, and unburned hydrocarbons. Hence, helping the vehicle meet environmental regulations.
7). Cold start performance.
The fuel injection pump delivers the right amount of fuel during startup. This helps the engine start more reliably and quickly in cold conditions.
The role of fuel injection in reducing emissions and improving fuel efficiency.
Fuel injection in reduces emissions and improves fuel efficiency by offering precise control over the air-fuel ratio, adjustment of air-fuel ratio depending on engine operating conditions and delivering fuel more efficiently and effectively to the engine cylinders among others.
This technology plays a significant role in reducing emissions and improving fuel efficiency in internal combustion engines. Fuel injection systems help optimize the combustion process by precisely controlling the amount of fuel delivered to the engine cylinders and the timing of injection events.
Therefore, leading to cleaner exhaust emissions and better fuel economy.
1). Precise control over the air-fuel ratio.
One key way fuel injection reduces emissions is by enabling more precise control over the air-fuel ratio compared to carbureted systems.
Maintaining the correct stoichiometric ratio of air to fuel ensures more complete combustion, minimizing the production of harmful pollutants such as carbon monoxide (CO), hydrocarbons (HC), and nitrogen oxides (NOx).
2). Adjust the air-fuel ratio based on engine operating conditions.
Additionally, fuel injection systems can adjust the air-fuel ratio dynamically based on engine operating conditions, further optimizing combustion efficiency and reducing emissions across a wide range of engine speeds and loads.
3). Delivering fuel more efficiently and effectively to the engine cylinders.
Fuel delivery is one factor of comparison between fuel injection and carburetor systems. Fuel injection contributes to improved fuel efficiency by delivering fuel more efficiently and effectively to the engine cylinders.
Unlike carburetors, which rely on suction to draw fuel into the intake manifold, fuel injectors spray atomized fuel directly into the combustion chamber, resulting in better fuel atomization and more even distribution.
4). Precise fuel metering.
This finer control over fuel delivery allows for more precise fuel metering, reducing wasted fuel and improving combustion efficiency. As a result, vehicles equipped with fuel injection systems typically achieve better fuel economy compared to carbureted counterparts, helping drivers save money on fuel costs and reducing their environmental footprint.
Overall, fuel injection technology plays a crucial role in modernizing internal combustion engines, enabling cleaner emissions and improved fuel efficiency to meet increasingly stringent environmental regulations and consumer demands for more sustainable transportation solutions.